Often depicted in media by historical pictures of coal miners with a pickaxe or prospectors panning for gold, the mining industry has not modernized, thinks the average citizen. This is an unfair and inaccurate depiction of one of the most innovative industries on the planet. Today, we use complex extraction processes and machines that are created for a specific task – like sorting different sizes of ore for crushing and automated ventilation systems for underground mines.
Sometimes the sought-after mineral is so small that it’s nearly invisible to the naked eye. This means mineral processing is a huge component of the mining industry, but it isn’t always top of mind when an average person thinks about mining.
We will need more mined materials and increasingly esoteric metals as society decarbonizes. For example, compared to a conventional car, building an electric car uses approximately six times the amount of minerals.1
Trends we’re seeing and work we’re doing
Due in part to the increased demand for minerals and metals, there is also an increasing requirement for new mines and brownfield expansions. Investors and consumers are both demanding more sustainably sourced products. So, how can we be more sustainable in the mining industry? We can start by increasing efficiency and reducing waste during mining and mineral processing. When the opportunity allows, a mine site, including its processing plants, can utilize renewable energy.
1 | Increasing Efficiency
One way to operate in a more environmentally friendly way is to ensure processing systems are running with maximum efficiency. A process that’s been working well for years might be due for a checkup to see if there are ways to optimize both the energy use and material yield.
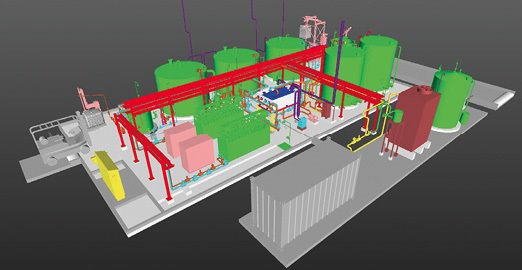
Over the last few years, we’ve seen a spike in demand for efficiency-related work – like energy audits and debottlenecking projects. If done right, sustainable designs and practices can save energy, drive costs down, and improve recovery rates. For example, a copper mine in Arizona completed a debottlenecking study and found they could save energy costs by modifying their grinding and crushing circuit. This also reduced their greenhouse gas emissions and increased their recovery.
How we handle materials before and during processing can also increase efficiency. Streamlining transportation or reconsidering what needs to be transported makes a big difference. For example, there is an underground gold mine in Turkey that has an underground crushing chamber. By beginning the minerals processing journey as close to the mined ore as possible, it maximizes materials handling efficiency.
2 | Reducing waste
We know that the natural resources on this earth are finite. The mining industry has a duty to operate within the concept of sustainable development. We must treat our resources responsibly. Resource scarcity can be lessened by reusing or recycling waste materials and tailings.
Many sites have deployed innovative ways to reuse water at mine sites. Roy Hill’s Pilbara operation in Western Australia built an aquifer recharge system. The mine site consists of a conventional open pit bulk mining operation with a 60 million tonnes per year processing plant. Managing groundwater is a consistent challenge for mine operators. Storing and recycling the water is the most sustainable option and mitigates any environmental risk to local flora and fauna. Our team managed the detailed design of a pipeline to transport dewatered saline water from the remote mine to an aquifer approximately 45 km away.
In the industry it is becoming more popular to re-process tailings or waste rock to extract other minerals (not the original sought after resource). A great example of this is a gold adsorption pilot plant, built to maximize gold recovery from tailings waste. The plant trialed back-end recovery of a new flotation tailings stream through the existing gold plant. The client wanted to know if the existing carbon-in-leach circuit, a part of the gold extraction process, had the additional capacity to accept flotation material and recover sufficient gold. The pilot plant was a success. Now the client will be able to replicate this tailings waste recovery solution, thus maximizing gold collection efficiency.
3 | Replace conventional energy sources
Energy is a key factor in processing plant operations. It is a major cost, often around a third of the total cost, and is becoming more critical as an environmental consideration. The plant can minimize energy consumption by using processes such as high-pressure grinding rolls and autogenous or semi-autogenous grinding or vertical milling.
Once a plant has reduced its energy consumption, the next step to becoming more sustainable is transitioning to a greener, cleaner energy source. Renewable energy in mining operations is becoming more common thanks to increasingly cost-effective energy storage. A great example is the rapidly maturing solar energy project from Alinta Energy. Stantec consulted on the design and construction of this solar energy project. When complete, it will provide up to 60 MW of generation capacity in the Pilbara region of Western Australia.
Where the industry is headed – new standards
It’s exciting to see how quickly the mining industry is evolving. Ten years ago, discussions around renewable energy or reusing tailings were rare. Now, we’re seeing mining companies being proactive and making these things happen every day. Even though many renewable energy projects are still in initial concept, permitting, and design stages, it’s great to see how much progress has been made in the last decade.
It’s very likely we will see greater regulation and licensing around energy efficiency, waste management, and overall, renewably energy or greenhouse gas emissions. Process plants traditionally measured by demand, schedule, grade, recovery, and yield, will likely have optimization and sustainability-related targets to hit as well (if they don’t already!) So, it’s important for mine owners and operators to act now to develop energy efficient and effective mineral processes. This will help them be more prepared for both the greater demand for minerals and metals and increased regulation in the future.
Stephen Beamond is Stantec’s regional leader for energy and resources in Queensland, Australia and internationally.
1. https://www.iea.org/data-and-statistics/charts/minerals-used-in-electric-cars-compared-to-conventional-cars